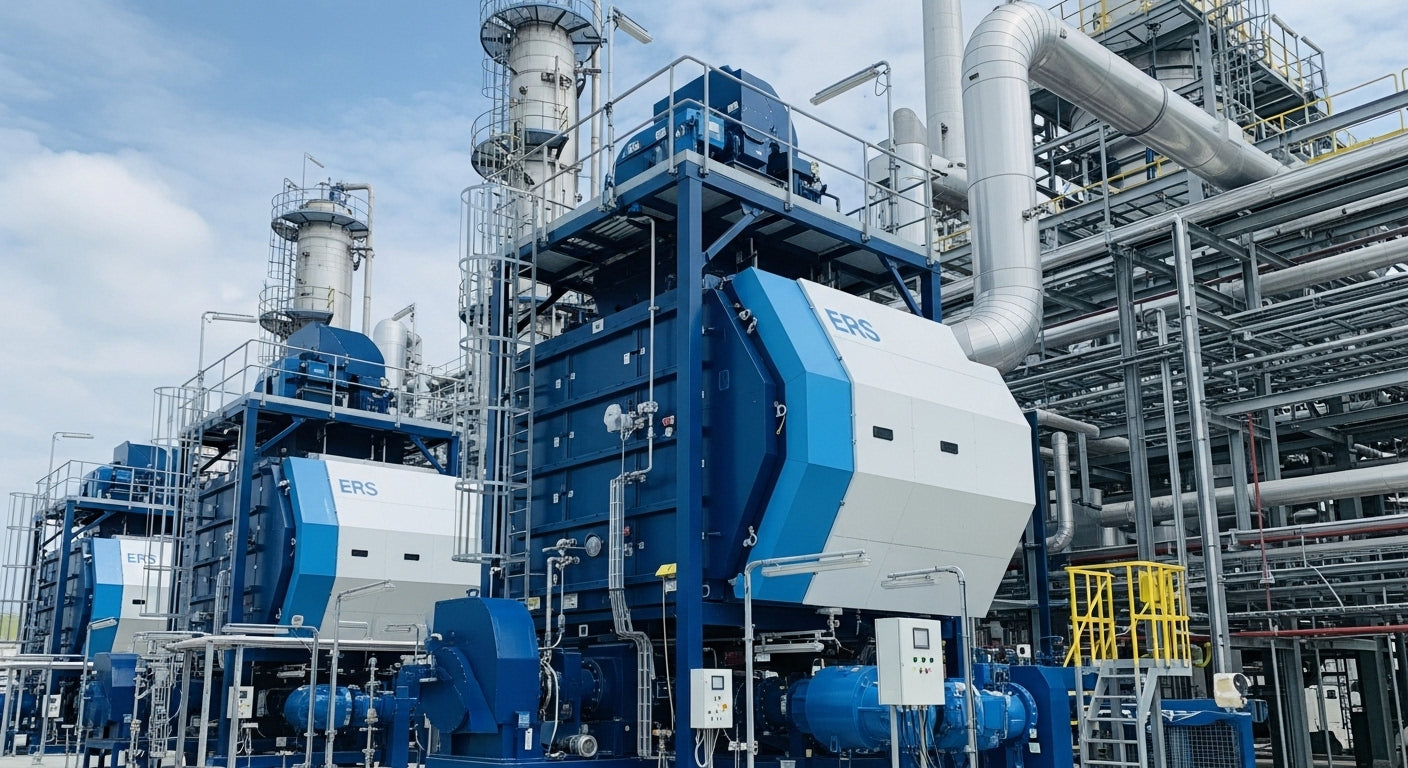
The Advantages Of Energy Recovery Systems
In the quest for operational efficiency and sustainability, industrial plants increasingly turn to energy recovery systems (ERS). These systems capture and repurpose waste energy, offering significant cost savings and environmental benefits. Implementing an ERS in an industrial setting can transform waste into a valuable resource, enhance energy efficiency, and reduce greenhouse gas emissions.
Understanding Energy Recovery Systems
Energy recovery systems are designed to reclaim energy otherwise lost in industrial processes. This waste energy can take various forms, such as heat, steam, or pressure. By capturing and repurposing this energy, ERS can provide power, heat, or cooling, reducing the need for additional energy inputs and cutting operational costs.
Key Components of Energy Recovery Systems
1. Heat Recovery Systems: These systems capture waste heat from combustion or chemical reactions. The recovered heat can preheat raw materials, generate steam, or produce electricity through cogeneration.
2. Steam Recovery Systems: Many industrial plants produce steam as a byproduct. Steam recovery systems capture and reuse this steam for heating, power generation, or other processes, reducing the need for new steam production.
3. Pressure Recovery Systems: In high-pressure gas or liquid processes, pressure recovery systems can harness the energy from the pressure drop, converting it into sound mechanical or electrical power.
Benefits of Implementing Energy Recovery Systems
1. Cost Savings: Industrial plants can significantly reduce their energy consumption by reusing waste energy, leading to lower utility bills and operational costs.
2. Environmental Impact: Energy recovery reduces the demand for fossil fuels, cutting greenhouse gas emissions and contributing to a cleaner environment.
3. Operational Efficiency: ERS can enhance process efficiency by providing additional energy sources and stabilizing energy supply, leading to more reliable and consistent operations.
4. Regulatory Compliance: Implementing ERS can help plants meet stringent environmental regulations and standards, avoid potential fines, and enhance their market reputation.
Steps to Implement Energy Recovery Systems
1. Energy Audit: Conduct a comprehensive energy audit to identify waste energy sources and quantify the potential for energy recovery.
2. Feasibility Study: Evaluate the technical and economic feasibility of various ERS options, considering factors like initial investment, payback period, and integration with existing systems.
3. System Design: Develop a detailed design for the chosen ERS, including specifications for equipment, control systems, and integration points.
4. Installation and Commissioning: Install and integrate the ERS components into the existing plant infrastructure. Conduct thorough testing and commissioning to ensure optimal performance.
5. Monitoring and Maintenance: Implement a robust monitoring and maintenance program to ensure the ERS operates efficiently and reliably over its lifespan.
Case Study: Success in the Automotive Industry
A leading automotive manufacturer recently implemented a comprehensive ERS in one of its production facilities. By installing heat exchangers to capture waste heat from the painting process and using them to preheat incoming air and water, the plant achieved a 15% reduction in energy consumption. Additionally, implementing a steam recovery system reduced the need for boiler-generated steam, leading to further cost savings and a significant decrease in CO2 emissions.
Driving Sustainability and Profitability with Energy Recovery Systems
Energy recovery systems (ERS) are powerful tools for industrial plants seeking to enhance efficiency and sustainability. Plants can achieve significant cost savings by capturing and repurposing waste energy, reducing their environmental impact, and improving operational reliability. Contact us to discuss the options available for your facility to save 15% or more on electricity costs.